Spiral Conveyors
Spiral conveyors move units of product vertically where floor space is limited or the product needs to be travelling through multiple floors of a facility. (See bucket elevators for vertical movement of bulk material). Spiral conveyors are available in a variety of materials and configurations, each with its own benefits and drawbacks.
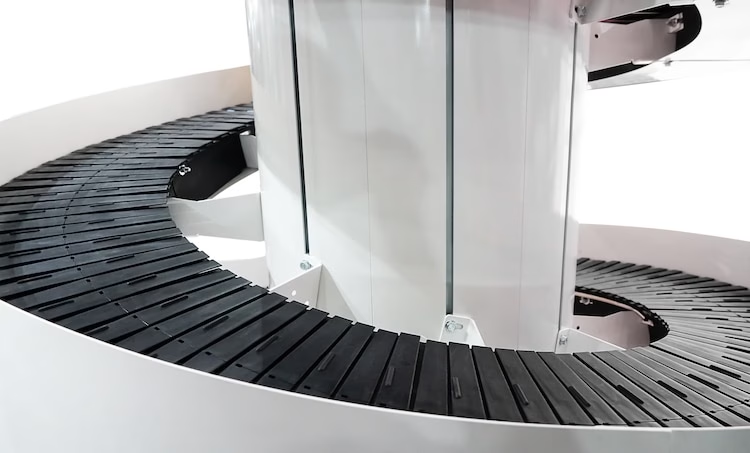
Materials
Spiral conveyors can be made from a variety of materials, each with its own strengths and weaknesses. The most common materials used in spiral conveyors are stainless steel, carbon steel, and plastic.
Stainless Steel
Stainless steel is a popular material choice for spiral conveyors because it is strong, durable, and easy to clean. Stainless steel is also resistant to corrosion, making it ideal for use in applications where materials are exposed to moisture or chemicals. However, stainless steel can be more expensive than other materials, and it may not be suitable for certain applications where weight is a concern.
Carbon Steel
Carbon steel is a less expensive alternative to stainless steel and is often used in applications where weight is a concern. Carbon steel is also strong and durable, but it is more prone to corrosion than stainless steel. To combat this, carbon steel can be coated or painted to protect it from moisture and chemicals. However, this can add to the cost and maintenance requirements of the conveyor.
Plastic
Plastic spiral conveyors are a lightweight and cost-effective solution for applications where weight is a concern. Plastic conveyors are also resistant to corrosion and can be easily cleaned. However, plastic may not be suitable for applications where materials are exposed to high temperatures or abrasive materials.
Configurations
Spiral conveyors can be configured in a variety of ways to meet the specific needs of each application.
Single Lane
Single lane spiral conveyors are the simplest and most common configuration. They consist of a single spiral that transports materials vertically between two levels, while the return belt makes a direct, vertical return to the infeed.
Dual Lane
Dual lane spiral conveyors are used when more than one product needs to be transported vertically. They consist of two spirals that are stacked on top of each other and run in opposite directions. Dual lane conveyors are ideal for applications where materials need to be separated or sorted.
Vibratory
Spiral conveyors are available in vibratory configurations, which will take up less footprint and use less energy than their belted counterparts.
Benefits
Space: Spiral conveyors make for an efficient use of space and can help to maximize floor space in a facility.
Efficiency: Spiral conveyors are efficient and can transport materials quickly and easily between multiple levels.
Versatility: Spiral conveyors can be configured in a variety of ways to meet the specific needs of each application.
Durability: Spiral conveyors are built to last and can withstand the rigors of daily use.
Drawbacks
Cost: Spiral conveyors can be more expensive than other material handling solutions, especially when made from stainless steel.
Maintenance: Spiral conveyors require regular maintenance to keep them operating at peak efficiency.
Limited Capacity: Spiral conveyors may have limited capacity, depending on the specific configuration and materials used.
Why ABM?
ABM is more than just a connection to OEMs. With over 20 years of experience in the industry, we have built a reputation for providing high-quality, reliable, and effective conveying solutions to a wide range of industries.
With a team of experienced engineers and technicians, we provide customized solutions to meet the specific needs of our customers. We work closely with you to understand your requirements and recommend the most suitable conveyance configuration for your application.
We offer ongoing service and maintenance for our packaging systems to ensure they continue to operate at optimal performance. Our technicians are knowledgeable and experienced, and are available to provide on-site maintenance, repair and support services.
Whether you are looking for a single piece or a cohesive system, ABM Equipment can help scale and automate your process. Contact us below to learn more about our services and how we can help you achieve your production goals.