Bag Break Stations
Bag break stations offer a convenient place to introduce bags, sacks, or drums into bulk handling or processing systems. They consists of a dump hopper, a frame to support the hopper, and a discharge chute to direct the material into the process equipment or conveyance line.
- Standard Bag Break Station: Some manufacturers have standard models that are made with some economies of scale and are thus more cost-effective. These usually have a port that you connect to an external dust collection system.
- Self-Contained Bag Dump Station: As seen pictured, this type of station includes an integrated filter to capture and contain the dust generated during the dumping process. The dust control system can be a simple filter or a more advanced cyclonic separator that removes dust particles from the air stream. This type of bag break station is used for all types of products when production wants to reduce waste or keep the air clean when there isn’t an external system they can port the equipment to. But they are necessary, for extra-fine or hazardous materials —like chemicals and pharmaceuticals—where stray particles are particularly dangerous.
- Mobile Bag Break Station: Bag breaks can be put on casters and be made detachable, but are most commonly connected to conveyance via a swivel arm. They’re most useful when a processor has limited space or wants to be able to have multiple fixed inputs without connecting them directly to the line.
- Custom Bag Break Stations: Bag break stations are relatively simple and can be customized to include specific features, such as special materials of construction, custom dimensions, or integrated dust control systems, like our Auto-Pulse Bag Dump.
Whether you need something out-of-the box or made just for your system, get in touch for the best solution for your process.
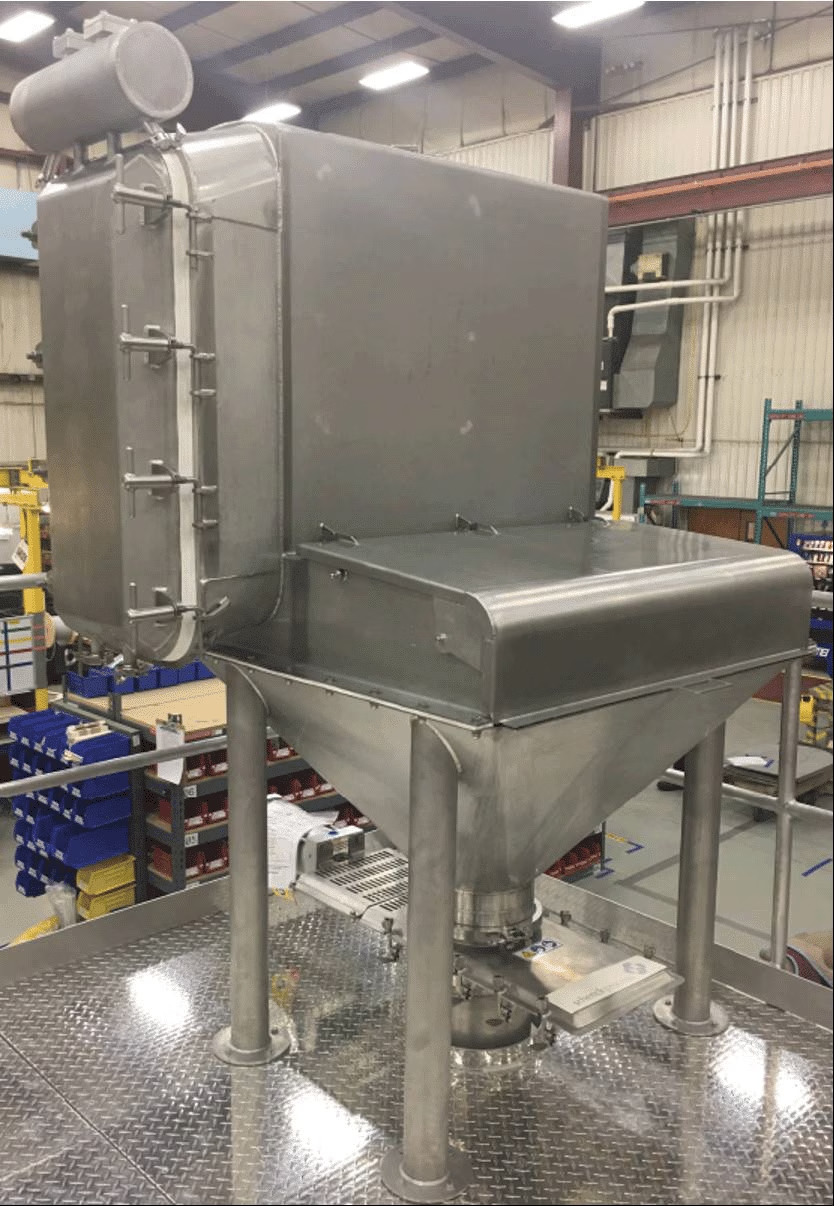
Features:
- 10 gauge formed carbon steel legs
- 12 gauge housing and hopper
- Integrated filter housing (jet pulses auto-clean the filter, returning product back into the process
- Carbon steel grate bag cups made of mineral reinforced nylon
- Fully-welded exterior
- Skip-welded interior
- Carbon steel bag cages (the bags themselves are made of 16 oz. singed dacron polyester with a convenient top removal snap band. The bag cup caulk is FDA-approved silicone sealant.)
For easy access, the bag break station includes a bolted 15″ x 28″ service door. It is also equipped with a top-mounted #12 SB fan with a 2 HP, 3600 RPM, TEFC 230/460 V/3PH motor, rotating in a clockwise direction when viewed from the back. The grate can be easily removed for maintenance and cleaning.
Options:
- Vacuum or Pressure
- The vacuum unit features a discharge flange that matches a Schenck Process probe box, while the pressure unit is equipped with a discharge flange that matches a Schenck airlocks.
- Both pressure and vacuum units can be equipped with a dust draw off hood, which includes a 4″ O.D. draw off stub instead of a dust filter.
- Aluminum or 304 stainless product contact surfaces
- Industrial grade epoxy interior
- GC24, CG80, or CG120 welds for product contact areas
- On/off switch and NEMA 12 prewire package for fan and filter operation
- NEMA 9 electrical components
- Latched/sealed inlet door
Features
- Integrated dust collector (jet pulse returns product to process)
- 7 gauge stainless housing & hopper with 3-A finish inside and out
- Hinged door with gas springs
- Ferrules mounted for CIP configuration
- Large openings for sanitary internal CIP
- Removable internal bag rest
- Hopper discharge to fit any airlock
- Stainless diaphragm bodies
- 304 stainless bag cages
- 16 oz. (454 g) singed polyester, side removal bags (3-A)
- Sanitary ferrule exhaust
Options
- Filtered and non-filtered configurations
- Non-filtered configuration uses a 4” (102 mm) O.D. ferrule dust port
- Filtered configuration uses a 5” (127mm) O.D. ferrule dust port
- Mount pad covers (welded on site)
- Magnetic internal bag rest
- Cartridge filter element
- Polished exterior welds
Whether you need an existing bag dump station modified or a new one built, we can deliver the ideal solution for your process with in-house design, fabrication, and installation. Give us a call or fill out the form below to learn how we can add value to your process.