Whether you’re closing down your brewery or beverage manufacturing facility, or need to free up space in your real estate asset, our professional brewery decommissioning services are here to assist. We specialize in the dismantling, removal, and scrapping of used brewing equipment and other beverage manufacturing equipment, regardless of its condition or location.
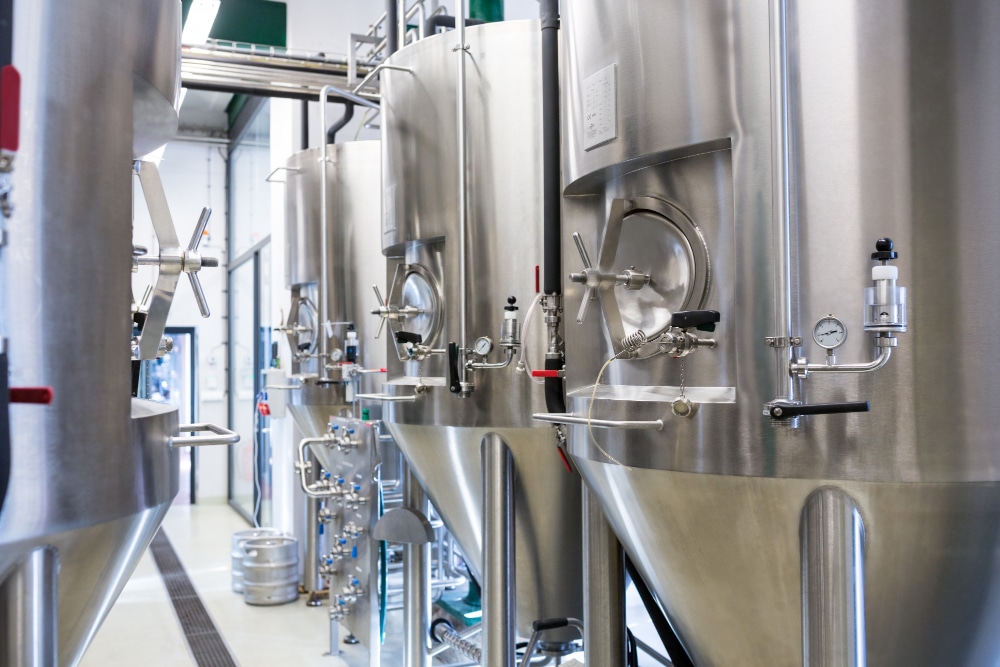