Flat Belt Conveyors
Flat belt conveyors are the simplest and most common of conveying methods but are used for relatively lower capacity and speed applications compared to other methods. They can be used on slopes up to a maximum of 20° but use on slopes is rarely advisable. Flat belt conveyors are available in endless configurations, which we source or construct, usually depending on where it’s cheaper to ship from. We provide all services required for the installation and maintenance of virtually any flat belt conveyors.
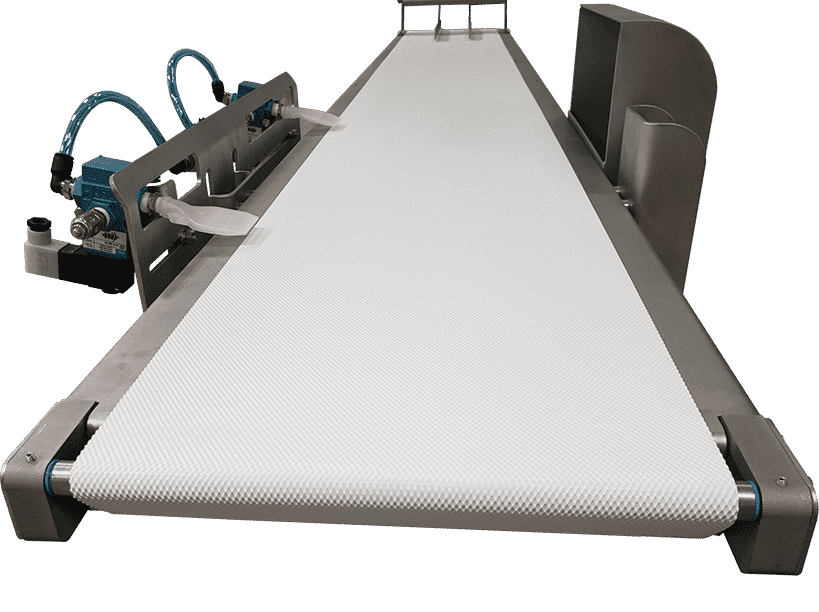
Drive Methods
Traditional Belt Conveyors (ie. friction/negative drive)
When most people think of belt conveyors they think of belt tensioned around drives and being moved by the friction between the belt and drive. This is the most common method but requires more maintenance and drive adjustment in heavy applications. This is because more weight means not only more strain on the belt, but more slippage and wear. Additionally, they take more work to clean in sanitary applications because tension has to be removed in order to clean under the belt. But for most applications the negative drive belt remains the most practical and cost-effective option.
Positive Drive Conveyors
Positive drive conveyors use direct force instead of friction to move belt; this is achieved with recessed notches in the belt and geared drives with cogs (or visa-versa). These cogs fit into the notched belt (or visa-versa) which is moved directly, without any slippage. Because this method does not require tension to operate, it doesn’t need to be adjusted as much and is easier to clean. An example is shown here, courtesy of Intralox.


Drive placement
Drives are placed at the head (discharge) whenever possible because that’s where they perform best. When driven at the tail, there is no direct force on the load-bearing side of the belt (you can’t convey boxes by pushing a rope they’re sitting on). The belt must be pulled, which means pulling the belt around the opposite side, inflicting double the wear because it’s being tensioned around two points.
There are, however, special applications where placing the drive at the tail will provide more value than it consumes. For example, if the belt is discharging into a sanitary environment, close proximity of gearboxes and non-sanitary components is not acceptable. It could also simply make more sense service-wise if the drive is inaccessible at the head.
Drives can also be placed in the middle of the belt in special circumstances, such as when you’re loading the belt in the center and swapping the conveyance direction to discharge at alternating sides.
Materials
Conveyor belts can be made of various materials depending on the product, including inter-linked plastic which can shift and convey about corners. Material type largely depends on product temperature, mass, abrasiveness, and sanitation requirements.
Most Common Material and Application Pairings
Metal – Filter, heat, bakery, de-oiling, de-watering
Rubber – (Most common type of belt), aggregate, packaging, most non-food applications
Plastic – Food
Fabric – Specialty applications (mostly obsolete)
Neoprene – Packaging (because of its oil-resistant nature)
Poly Belt – Packaging (because of its oil-resistant nature)
Linked plastic (modular) – When practical because of its affordability, (does not bode well in high-impact applications
Pulley types
Drive pulleys can be crowned (wider in the center) to help keep the belt from walking, and standard pulleys can be placed in a number of configurations to handle slack. Crowned pulleys are most common for receiving raw product like beets & potatoes and are not necessary in positive drive applications.
Frame configurations
Conveyor belts may have a number of different frame configurations depending on what the application yields itself to. But whether you can use hollow support points depends on regulations. (FDA allows hollow support points, USDA does not.)
Beds
The beds for conveyors are usually flat and only meant to support the belt, but they can also be fitted with sidewalls to help contain and protect product. But because of the contact between side-walls and product, trough belt conveyors are used for particularly abraisive or delicate materials or foods. Trough belt conveyors are also preferred over walled flat conveyors in sanitary applications because they’re much easier to clean.
Reject Systems
Flat-belts can be fitted with a huge variety of rejects, all of which we build for the application. The techniques used could include diverters, push-arms (pneumatic or electric), drop-panels, air blast, magnets, and others. In bulk applications where rejection of good product with the bad cannot be avoided, accuracy must be maximized to reduce the effect.
From conveyor repairs to complete system design and integration, we help move bulk dry goods efficiently. Whether it’s food, pharma, or industrial, there is a best method for moving every product and we deliver the appropriate level of speed and gentleness, all backed by 24/7 service.
Get In Touch
Tell us about your project and we’ll provide a quote, go over your options, or simply point you in the right direction.
"*" indicates required fields

Industries
Warehousing & Distribution
Manufacturing
Aerospace
Automotive
Parcel Handling
Cabinetry & Furniture
Aggregate
Agriculture
Baby food
Bakery
Beverage
Building materials
Cannabis
Cereal & Grains
Chemicals
Chemicals & Fertilizer
Confectionery
Dairy
Distillery
Electronics
Energy
Food
Fruit & Vegetables
Grocery / Point of Sale
Hemp
Laboratory
Livestock
Manufacturing
Meat
Medical / Veterinary
Nutraceuticals / Supplements
Nuts
Packaging
Personal Care
Pet Food
Pharmaceutical
Plastics
Poultry
Ready Meals
Recycling
Red Meat
Seafood
Shipping
Snackfood
Spices, Syrups & Sauces
Tobacco
Warehousing, Transport, & Logistics
Waste
More Conveyors
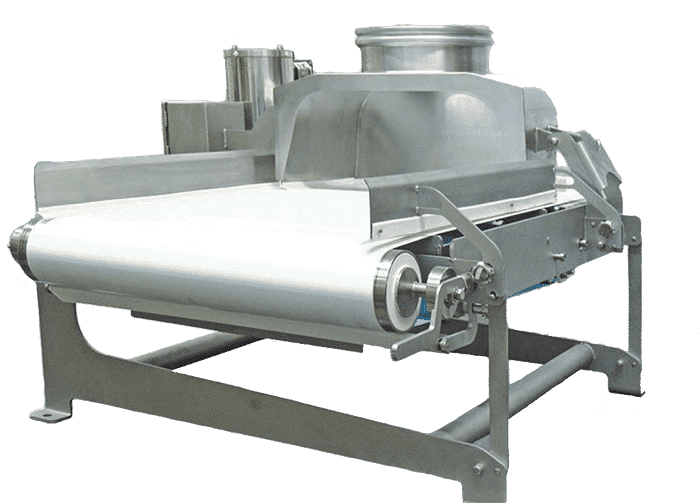
Weighbelts
Weighbelts are flat belt conveyors with weighbars beneath the belt to measure product flow. Knowing product weight and convey-rate, weigh-belts precisely meter product into the dryer by communicating with up-stream equipment and adjusting speed. Weigh-belts are critical between the shredder and the dryer because consistent feed-rates are critical for any continuous-flow herb drying processes to prevent burning product or leaving wet spots. They can also be used in various parts of the process to provide a number of data points such as moisture weight-loss.
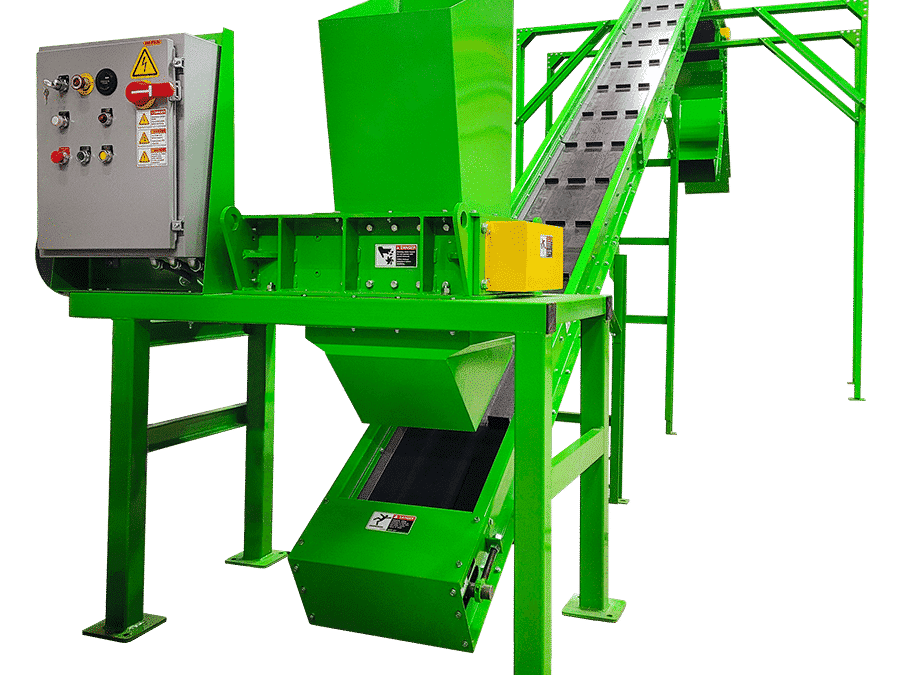
Herb Shredders
Shredders slice herb it into small, homogenized particle sizes in preparation for drying. Shredders are preferable over mills for wet product because mills crush instead of cut; crushing inflicts unnecessary damage, makes screens difficult to clean, and compacts the flower which further reduces drying efficiency.
Our high-throughput, super-sturdy herb shredders come with variable controls to accommodate any drying method. They’re available in various sizes from 1–400 HP, with maximum throughputs ranging from 100–10,000 lbs./hr., and optionally available in stainless.
Most dryers will perform best with particle sizes between 3/4 and 1/4″, with the latter being ideal for ABM solutions. 1/4″ shred carries the added benefit of being suitable for extraction, allowing extractors to skip the mill. ABM provides turn-key integration and 24/7 emergency support for all components and systems in our wheelhouse.
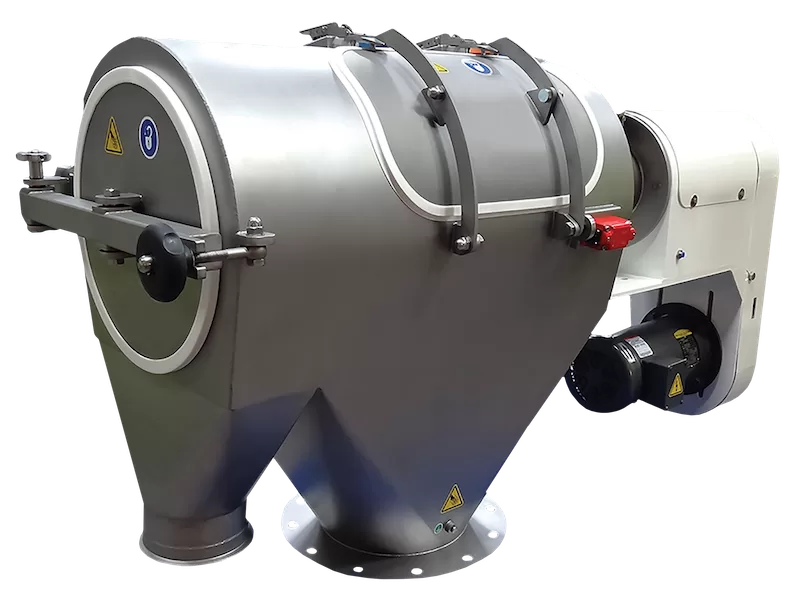
Herb Sifters
ABM’s Herb Sifters remove stalks and stems from premium biomass with far greater speed & precision than human hands, buckers, or other mechanical options. They are low-maintenance, easy to clean, and extremely long-lasting.
Using flow-assists and screw feeders to control the flow of shredded bud into the separating chamber, it uses specially-shaped paddles to propel it against the surrounding sieve. This pushes the desirable fines out through the apertures while the over-sized stems are rejected.
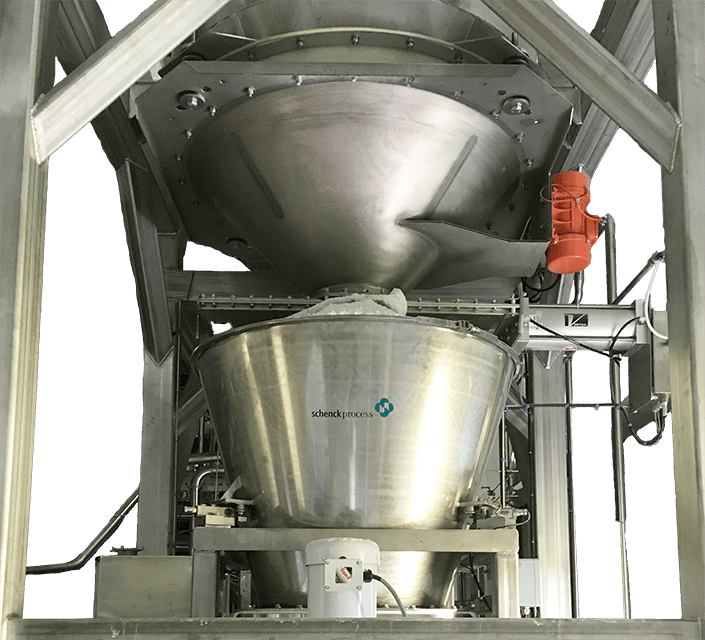
Surge Hoppers
Surge hoppers, or storage hoppers, stabilize product flow between continuous-flow and batch processes to maintain the system’s ability to run continuously despite some equipment needing change-time. They are commonly used before mixers to allow time for batches to finish, and before bulk bags to allow time for bag changes. These powder-coated or stainless hoppers can come in any shape or size required and come equipped with flow-aids to ensure smooth flow and prevent product from bridging.